Nachhaltigkeit im Fokus – Beispiele aus der Praxis
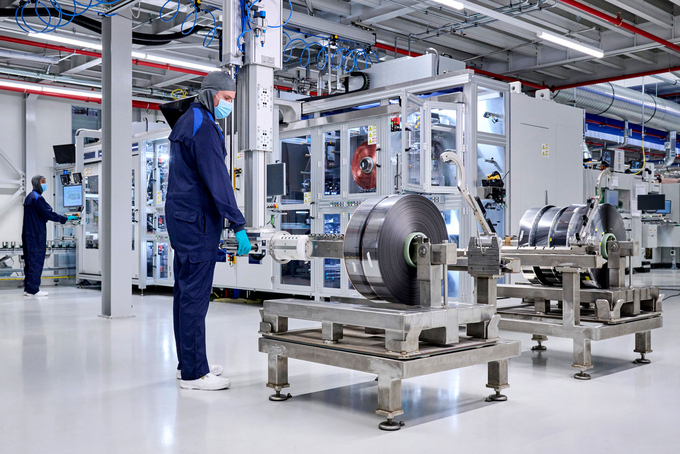
Batteriezellen für Elektrofahrzeuge lassen sich sowohl umweltschonend als auch energieeffizient produzieren – und wiederverwerten. Beispiele aus der Praxis gibt es bereits.
Von Josef Stelzer, IHK-Magazin 03/2025
Die Lithium-Ionen-Batterien moderner Elektroautos bestehen aus Tausenden einzelner Batteriezellen. Solche Zellen dienen als Stromspeicher und sorgen für unterschiedliche Fahrleistungen, Reichweiten und Ladezeiten – je nach Technologie und Anzahl der eingebauten Zellen. Sie bilden gewissermaßen das Rückgrat der Elektromobilität.
Doch die Herstellung der zumeist zylindrisch geformten Zellen ist aufwendig und kostspielig, zumal wertvolle Rohstoffe wie Lithium, Kobalt, Nickel, Grafit oder Mangan erforderlich sind. Nachhaltige Herstellungs- und Recyclingverfahren helfen beim Ressourceneinsatz und tragen überdies zum Klimaschutz bei. Die Automobilhersteller BMW und Mercedes-Benz zeigen, wie sich dies in der Praxis umsetzen lässt.
Pilotfertigung in Parsdorf
Das 2023 eröffnete BMW Group Kompetenzzentrum für Batteriezellfertigung in Parsdorf bei München, kurz CMCC, dient als Pilotfabrik für die Muster von Batteriezellen. „In unserer Pilotfertigung konzentrieren wir uns darauf, kritische Rohstoffe und Energiebedarfe zu reduzieren, Lösungsmittel zu vermeiden und innovative Ansätze für die Zirkularität von Batterierohstoffen zu entwickeln“, sagt CMCC-Leiter Bernd Wächtershäuser. Die anfallenden Reststoffe stehen, falls technisch möglich, für die Wiederverwertung zur Verfügung.
Für die eigentliche Großserienfertigung der Zellen werden künftig die chinesischen BMW-Partner CATL und EVE Energy an ihren ungarischen Standorten sorgen. Dabei könnten auch die im Parsdorfer Werk gewonnenen Erkenntnisse über Produktionsverfahren und Ressourceneinsatz einfließen.
Dünner als ein Spinnennetz
Die Fertigung der neuen Rundzellen, die einen einheitlichen Durchmesser von 46 Millimetern und Längen von 95 oder 120 Millimetern aufweisen, beginnt mit der Herstellung der Elektroden, also von Anode und Kathode. Dabei wird das Grundmaterial, das unter anderem aus Grafit für die Anode und Nickeloxiden für die Kathode besteht, präzise dosiert und gemischt.
Der dabei entstehende „Slurry“ dient zur Beschichtung hauchdünner Metallfolien. Diese Folien sind nur wenige Mikrometer dick, also dünner als die Fäden eines Spinnennetzes. Die Dicke der Beschichtung bewegt sich ebenfalls im Mikrometerbereich. Teilweise kommen Recyclingmaterialien zum Einsatz.
EMAS treibt Nachhaltigkeit
In der Zellmontage werden die beschichteten Folien – kalandrierte Elektroden in der Fachsprache – zu sogenannten Jelly Rolls gewickelt und in das Zellgehäuse eingesetzt. Nach der Befüllung mit einem Elektrolyten, der für den Stromfluss erforderlich ist, sowie dem erstmaligen Aufladen folgt die abschließende Funktions- und Qualitätsprüfung.
Vergangenen November 2024 erhielt die Parsdorfer Fabrik die europäische Umweltzertifizierung EMAS. EMAS steht für Eco-Management and Audit Scheme und gilt als anspruchsvollstes Umweltmanagementsystem weltweit. „Wirtschaftlicher Erfolg und nachhaltige Betriebsabläufe sind kein Widerspruch, ganz im Gegenteil. Das beweist jeder Betriebsstandort, der sich der EMAS-Einführung stellt“, betont Manfred Gößl, Hauptgeschäftsführer der IHK für München und Oberbayern.
Recycling als Kostenbremse
Das BMW-Werk wird fossilfrei und zu 100 Prozent mit erneuerbaren Energiequellen betrieben. Für die Wärmeversorgung im Gebäude kommen Grundwasser- und Luftwärmepumpen sowie Abwärme aus verschiedenen Herstellungsprozessen zum Einsatz.
Im niederbayerischen Kirchroth errichtet BMW derzeit ein Kompetenzzentrum für Batteriezellrecycling. Hintergrund: Die Rohstoffe für die Zellen, etwa Lithium und Kobalt, aber auch Grafit, Mangan, Nickel oder Kupfer, zählen zu den größten Kostenfaktoren in der Zellfertigung. Innovative Recyclingverfahren können erheblich dazu beitragen, die Kosten im Griff zu behalten. In der 2. Jahreshälfte 2025 soll der Aufbau der Produktionsanlagen starten.
Geschlossener Kreislauf
BMW setzt in Kirchroth auf das selbst entwickelte Direktrecycling, bei dem die bisher übliche energieintensive chemische oder thermische Aufbereitung entfällt. Das innovative Verfahren ermöglicht es, Reststoffe aus der Batteriezellfertigung sowie ganze Batteriezellen mechanisch in ihre Bestandteile zu zerlegen und für neue Zellen zu verwenden. „Mit dem neuen Kompetenzzentrum für Batteriezellrecycling erweitern wir unser Inhouse-Know-how um einen weiteren Baustein. Von der Entwicklung über die Pilotproduktion bis zum Recycling schaffen wir einen geschlossenen Kreislauf für Batteriezellen“, sagt Markus Fallböhmer, Leiter der BMW-Batterieproduktion.
Sortenrein extrahiert
Die Mercedes-Benz Group arbeitet ebenfalls an der Wiederverwertung. Im baden-württembergischen Kuppenheim eröffnete sie im Oktober 2024 eine Batterierecyclingfabrik. Ein mehrstufiger Prozess sorgt dort zunächst für die sortenreine Aufteilung in Kunststoffe sowie in Kupfer, Aluminium und Eisen. Im 2. Schritt extrahiert das Verfahren Materialien wie Kobalt, Nickel und Lithium.
6.800 qm Photovoltaik
Der Recyclingprozess im Kuppenheimer Werk soll insgesamt weniger energieintensiv sein als vergleichbare Methoden und geringere Abfallmengen erzeugen. Für den Betrieb der neuen Fabrik kommt ausschließlich Grünstrom zum Einsatz, wobei die Dachfläche des 6.800 Quadratmeter großen Produktionsgebäudes mit einer Photovoltaikanlage ausgestattet ist.
2030: zu 25% gebrauchte Rohstoffe
Zum Thema Recycling hat der europäische Umweltverband Transport & Environment (T&E) im Rahmen einer Studie interessante Resultate ermittelt. Demnach könnte Europa ab 2030 jährlich bis zu einem Viertel der für die Batterieproduktion erforderlichen Rohstoffe aus der Wiederverwertung gebrauchter Batterien decken. Die zurückgewonnenen Materialien dürften den Berechnungen zufolge für die Batterien von 1,3 bis 2,4 Millionen neuen Elektroautos ausreichen. Zum Vergleich: 2024 wurden in Deutschland rund 400.000 vollelektrische Pkws neu zugelassen.
Die Problemlöser
Knappe Ressourcen, Digitalisierung, Klimaschutz – das sind nur einige der gewaltigen Probleme, vor denen wir stehen. In Oberbayern gibt es zahlreiche Unternehmen, die diese Herausforderung annehmen: Sie entwickeln kluge Lösungen für die drängenden Aufgaben unserer Zeit. Das IHK-Magazin stellt diese Problemlöser in einer Serie vor.
Neugierig auf weitere Problemlösungen? Dann hier stöbern:
- Problemlöser ECOFARIO: Das Wunder muss warten
ECOFARIO-Gründer Sebastian Porkert ist ein Problemlöser: Er hat eine Technik entwickelt, um gefährliches Mikroplastik aus dem Wasser zu fischen. Jetzt kämpft er um die Finanzierung – und um Unterstützung durch die Politik.
- Problemlöser Energyminer: Schwimmende Kraftwerke
Das Potenzial der Wasserkraft zur Stromerzeugung ist längst nicht ausgeschöpft, findet das Start-up Energyminer – und setzt auf Kraftwerke in Fließgewässern.
- Problemlöser WYE: Die Natur als Vorbild
Das Start-up WYE hat einen Werkstoff für Möbel entwickelt, der sich komplett recyceln lässt. Die beiden Gründer arbeiten an einem geschlossenen Kreislaufsystem – ohne Müll.